摘要:本文以新一代歼击机为背景,分析了配套新成品研制过程质量监控的重要性和必要性,研究了国内外做法,以及美国国防采办要求和相关标准。基于以往型号经验,构建了依托技术质量审查,与里程碑评审关联,以“条目化表单”、“成熟度监控”和“前置性控制”为特点的量化监控模型。明确了产品级PDR、CDR、FRR、FCA/SVR、PCA的具体审查内容,制定近300项质量监控项目,并已组织开展了14轮次监控,掌控过程质量成熟度变化;分析了10万余项质量数据,推进预防性质量管理和供应商研制质量评价;提前发现、处置了风险和问题5000余项,在里程碑评审前设置“准入审查”和“预审查”,提升了评审质量和效率。满足了型号质量保证要求,得到广泛推广应用。
关键词:配套新成品;质量;量化;监控;审查
引言
作为型号总质量师单位,成都所不但要开展飞机总体研发质量控制,同时还要开展对配套新成品研制的质量综合管理,其中一个重要方面就是新成品研制过程质量监控。以往型号采用质量复查、质量检查等方法开展了大量工作,满足了型号研制要求,积累了丰富的经验。面对新一代歼击机配套新成品研制技术新、状态繁、周期紧、问题多、影响大的新特点和从“定性管理”向“定量管理”提升的新要求,需要在此基础上,进一步加以完善。
本文以新一代歼击机为背景,分析了配套新成品研制过程质量监控的重要性和必要性,研究了国内外做法,以及美国国防采办要求和相关标准。基于以往型号经验,构建了依托技术质量审查,与里程碑评审关联,以“条目化表单”、“成熟度监控”和“前置性控制”为特点的量化监控模型。明确了产品级PDR、CDR、FRR、FCA/SVR、PCA的具体审查内容,制定近300项质量监控项目,并已组织开展了14轮次监控,掌控过程质量成熟度变化;分析了10万余项质量数据,推进预防性质量管理和供应商研制质量评价;提前发现、处置了风险和问题5000余项,在里程碑评审前设置“准入审查”和“预审查”,提升了评审质量和效率。满足了型号质量保证要求,得到广泛推广应用。
1 问题提出
1.1 重要性和必要性
歼击机作为典型的航空武器装备,具有参研单位广、影响因素多及协作配套关系复杂等特点。经统计分析,配套成品故障占飞机外场问题的比例在80%左右,对整机质量影响显著;国际范围内先进歼击机配套成品总价值占飞机总价值的比例均在70%以上,美国F-22战机更已接近85%。同时,配套新成品研制和飞机研制存在复杂的输入输出关系和阶段转换的条件关系,从产品交付和研制程序上,直接制约着飞机研制进度。这些都充分表明,配套新成品研制对飞机整机研制项目的质量、成本和进度等都有着至关重要的影响。
新一代歼击机研制技术跨代提升,且很多是通过研发新成品(包括软件)来实现,导致部分成品的新技术成熟度不足即应用于工程实际。创新的研发管理模式,如全数字化MBD技术应用、多学科综合循环迭代优化、数字分析仿真验证等,对质量、进度的要求更高,并分解传递至成品,导致配套新成品研制技术新、状态繁、周期紧、问题多,面临着技术和管理上巨大的挑战和风险。为提前发现研制风险,并加以处置,需要建立配套新成品研制过程质量、成本、进度等项目管理多方面指标,并开展过程监控。
1.2 国内外先进做法、要求及需要开展的工作
在配套新成品研制过程质量监控方面,以往型号采用质量复查、质量检查等方法开展了大量工作,满足了型号研制要求,积累了丰富的经验。面对新一代歼击机配套新成品研制技术新、状态繁、周期紧、问题多、影响大的新特点和从“定性管理”向“定量管理”提升的新要求,需要在此基础上,进一步加以完善。
通过分析研究美国国防采办生命周期活动和流程,发现其做法是:通过一系列前置性的审查活动开展过程监控,并与里程碑评审紧密关联,以监控审查控制评审准入。以首飞里程碑前项目监控要求(如图1示意)为例,首先通过8个月的IPT团队级审查,监控、确认项目成熟度,在监控审查的基础上开展准入审查后,专家组进行2个月的预审查,梳理提出问题,再次准入审查后进入正式评审,确认问题的处置情况。

图1 美国国防采办流程中首飞里程碑前项目监控要求
以多轮审查的形式来开展过程质量监控的思路值得借鉴,但是如上例的审查流程周期较长,尤其是团队级审查和专家组预审查均以现场会议的形式进行,在新一代歼击机紧张的研制周期背景下无法照搬应用,需要在操作层面上,结合型号实际情况进一步改进,如采取更为高效的监控审查形式。
另外,通过对国内外相关标准[1]、[2]、[3]、[4],包括美国国防部MIL-STD-1521B《系统、设备和软件的技术审查和审核》、美国电子工业协会EIA IS-632《系统工程》、美国电气电子工程师学会IEEE P1220《系统工程》以及GJB 3273《研制阶段技术审查》等的研究发现,这些标准规定了一系列技术质量审查项目(如表1),但是没有具体规定这些审查项目的内容,也就是过程质量监控的项目、指标,需要结合新一代歼击机特点全新构建。
表1 相关标准规定的技术质量审查项目
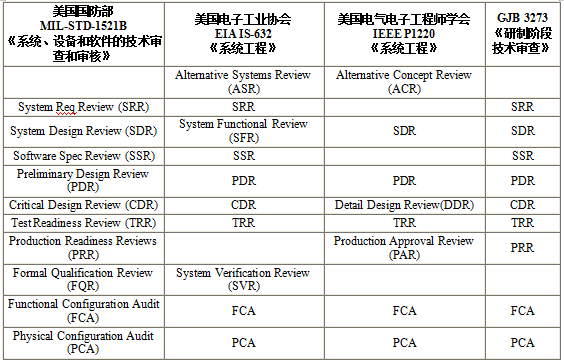
2 基本思路
在以往型号经验基础上,结合国内外先进做法和相关标准研究,适应新一代歼击机技术特点和管理模式,完善构建依托技术质量审查,与里程碑评审关联,以“条目化表单”、“成熟度监控”和“前置性控制”为特点的配套新成品研制过程质量量化监控模型。(如图2)。
(1)条目化表单
在监控指标和要求的体现形式上,由以往清理问题为主的复查报告模板,向监控状态为主的审查Checklist条目化表单改进。
(2)成熟度监控
在监控和分析工作流程上,由以往基于问题处置跟踪的监控,向依托多轮审查、深入过程的质量指标状态成熟度监控改进。
(3)前置性控制
在监控与里程碑评审的关联上,由以往问题和归零情况汇总,向基于监控控制准入并开展预审查的前置性控制改进。
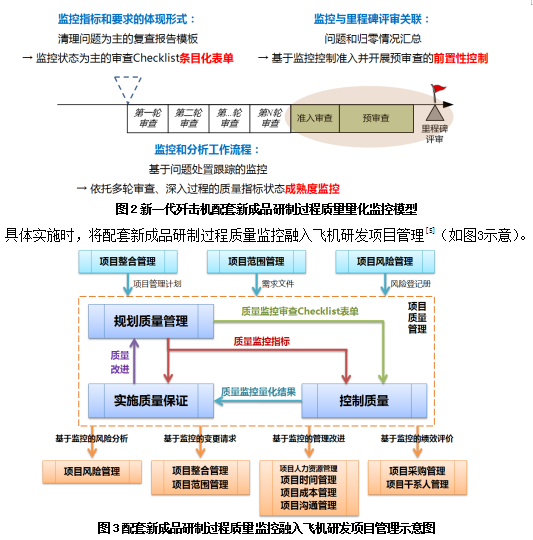
依据项目整合管理、项目范围管理、项目风险管理等项目管理工作输出的项目管理计划、需求文件和风险登记册等文件,制定质量监控指标和质量监控审查Checklist表单,开展质量监控,并以量化统计分析结果指导开展质量改进。基于研制过程质量量化监控开展风险分析、变更请求、管理改进和绩效评价,其结果分别为项目风险管理,项目整合管理、项目范围管理,项目人力资源管理、项目时间管理、项目成本管理、项目沟通管理,项目采购管理、项目干系人管理等项目管理工作提供依据和输入。
3 具体做法
在新一代歼击机研制之初,便将配套新成品研制过程质量量化监控工作纳入型号研制质量策划[6],按照构建的监控模型,随研制进展“边研制、边创新、边实践”,逐渐丰富要求和落实实施。
基于装备研制程序,在里程碑评审前依托技术质量审查,设置质量监控(如图4示意),包括F阶段研制质量监控(依托初步设计审查PDR)、C阶段研制质量监控(依托C阶段关键设计评审CDR)、首飞前研制质量监控(依托首飞准备状态评审FRR)、S阶段研制质量监控(依托S阶段关键设计评审CDR)、设计鉴定前研制质量监控(依托功能技术状态审核FCA/系统验证评审SVR)和生产定型前研制质量监控(依托物理技术状态审核PCA)等共六类。
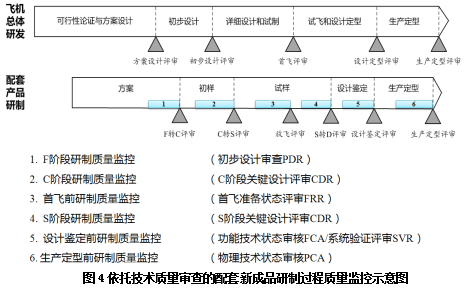
纳入型号质量师系统办公室工作,开展了对新一代歼击机56家新成品配套单位的现场调研,沟通协调制定的质量监控要求和流程。梳理了1300余项问题,统计分析问题的质量影响因素,结合研制过程质量控制要求,以此为依据构建质量监控项目和具体表单。
3.1 条目化表单
对上述六类配套新成品研制过程质量监控,共策划、部署了近300项监控项目(如表2),明确了产品级PDR、CDR、FRR、FCA/SVR、PCA的具体审查内容,以Checklist条目化表单的形式呈现,并落实在型号专用文件中。具体的审查项目主要分为3类:一是聚焦工作项目,审查应完成的工作项目是否已完成;二是聚焦交付物,审查应形成的交付物是否已形成;三是聚焦合格标准,审查应达到的合格标准是否已达到,以此明确监控要求。
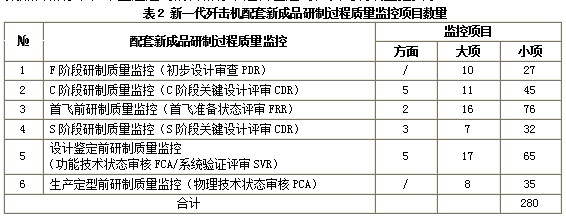
条目化表单的形式提高了监控要求的完整性,避免缺漏项;同时结构化的形式较以往的复查报告更加清晰、易操作,对照表单填报结果数据即可;方便对监控结果进行量化的统计分析,提升监控效果。
3.2 成熟度监控
梳理明确具体的监控审查及数据传递、统计、分析的流程和方法,落实在型号专用管理文件中,并纳入型号研发流程和质量师系统工作计划。现已按照新一代歼击机研制进展,针对全机400余项新成品,组织开展了14轮次的监控审查工作(如表3)。
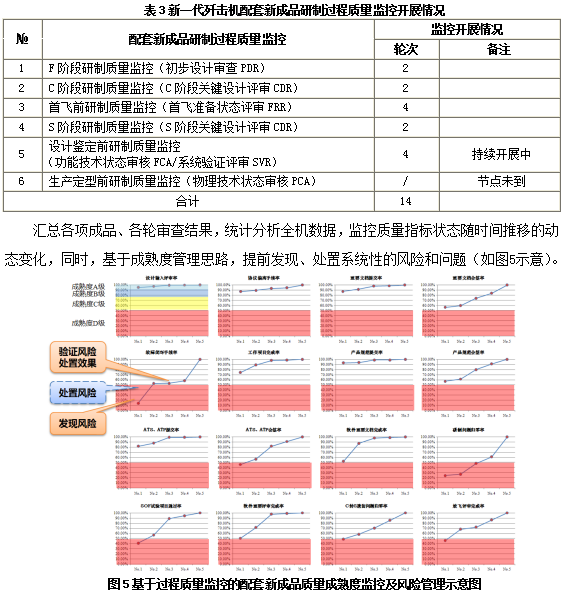
根据研制过程质量控制要求及历史经验数据划定成熟度等级。如首飞前研制质量监控(首飞准备状态评审FRR),划定第一轮审查时指标结果低于50%为成熟度D级、50%~75%为成熟度C级、75%~90%为成熟度B级、高于90%为成熟度A级[7]。分析某一项指标实际情况处于成熟度D级,则认为此项指标按要求实现存在风险,并启动相关风险分析和处置工作,分析存在问题,针对性采取纠正措施,并利用动态化质量监控验证措施执行效果。
基于结构化的审查监控数据,还可以对某一项指标在某个时间点,各家配套单位、每项成品的质量状态进行监控,并完成供应商级、产品级的风险和问题的识别、分析、处置和效果评估。
3.3 前置性控制
基于配套新成品研制过程质量监控,在新成品里程碑评审前设置“准入审查”和“预审查”(如图6示),提升里程碑评审的质量和效率。以“准入审查”,保证评审具备基本条件。以“预审查”清理状态、梳理问题,正式评审中确认“预审查”提出问题的处置情况。
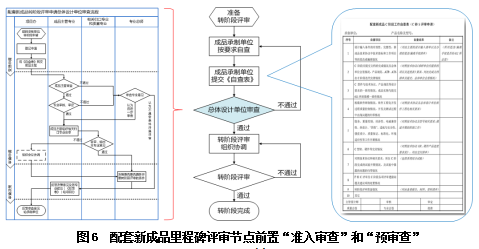
4 取得效果
适应新一代歼击机研制特点和要求,基于以往型号的配套新成品研制过程质量监控经验,结合实际技术问题的质量影响因素分析,按照研制过程质量控制要求,建立了依托技术质量审查的配套新成品研制过程质量监控的Checklist条目化表单,即明确了产品级PDR-CDR-FRR-FCA/SVR-PCA的具体审查内容。
明确了配套新成品研制过程质量成熟度监控,及前置性准入审查和预审查的具体流程和方法,并组织开展实施,发现、处置问题5000余项(如表4)。通过量化的质量指标成熟度监控,更为清晰明了地、提早掌控研制过程实际的质量状态,以帮助发现、处置系统性问题和风险,并向型号行政指挥系统、设计师系统提供决策支持,同时支撑里程碑评审质量和效率提升。
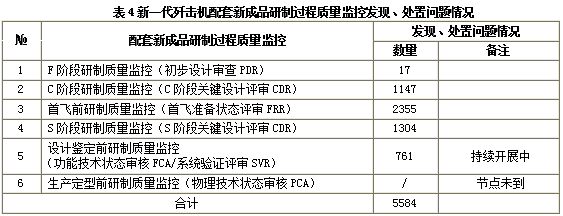
配套新成品研制过程质量量化监控积累了10万余项的研制过程质量数据,支撑型号质量知识库构建;保证研制过程质量翔实、清晰、完整“可追溯”;辅以知识推送,与工作包有效关联,发挥质量支持作用;数据智慧挖掘,预判质量趋势、鼓励流程改进,推进预防性质量管理;为供应商研制质量绩效评价提供数据支持。
另外,通过对监控结果数据的分析,还可以推进研制过程质量量化监控模型和实施流程的“自我完善”,如根据监控结果,针对性完善监控项目指标,调整对某项指标的关注程度,调整成熟度等级划分标准等。
通过配套新成品研制过程质量量化监控,在技术跨代提升、研制周期显著缩短的情况下,保证了新一代歼击机过程质量受控,满足了型号质量要求和研发系统工程对质量保证工作的要求[8]。成果提升为所标(作业文件)7份,在枭龙双座、翼龙II等型号研发项目质量管理中得到推广应用。同时,集团公司组织我所牵头,以本成果为基础,开展面向三型重点型号的质量保证能力提升工程,正在航空工业范围内得到推广应用。
配套新成品研制过程质量量化监控是成都所“型号精益研发质量保证体系”(获中国质量奖提名奖)核心能力的重要内容,同时支撑了《动态化条目化的重点型号研制过程技术质量审查创新与实践》集团公司管理创新成果一等奖、《重点型号配套新成品研制质量量化评价探索与实践》中国质量学术与创新论文二等奖等一系列优秀成果和论文形成,在《中国航空报》、《中国质量报》、四川电视台等多家媒体得到宣传报道,成为新一代歼击机研发质量管理的亮点。
5 发展展望
新一代歼击机配套新成品研制过程质量量化监控实际工作是“边研制、边创新、边实践”,需要进一步将成果标准化,并向航标、国军标提升。
另外,质量监控数据传递和分析现状是“EXCEL传递、统计和分析”,效率低,拟融入成都所“智慧院所”建设,实现数据多维度自动分析和质量成熟度趋势智能评估,并积极谋求建立跨研制全线的基于QBOM质量监控数据包的质量量化监控信息化系统。
同时,进一步加大成果推广应用,尤其是面向成都所总装集成交付无人机系统项目,以成品研制过程质量量化监控支撑型号的供应链管理和供应商研制质量量化评价。
参考文献
[1] 美国国防部MIL-STD-1521B《系统、设备和软件的技术审查和审核》
[2] 美国电子工业协会EIA IS-632《系统工程》
[3] 美国电气电子工程师学会IEEE P1220《系统工程》
[4] GJB 3273《研制阶段技术审查》
[5] (美)项目管理协会project management institute. 项目管理知识体系指南A guide to the project management body of knowledge,2013
[6] 蒋成、杨超、任为民.装备研制质量策划与实践.航空标准化与质量,2012(2):5~8
[7] 蒋成、杨超. 军机精益研发质量保证体系的建设.中国质量,2015(9):122~125
[8] 国际系统工程协会international council on systems engineering.系统工程手册Systems engineering handbook,2015