摘要:本文介绍了航空装备质量归零的现状,从质量问题等级划分不清、眼睛向外导致问题原因定位不准确、过于强调快速归零导致归零不彻底、举一反三不全面等四方面阐述了问题,提出了建立问题分级管理、建立归零最佳实践、建立典型问题管理原因分析机制、建立质量问题归零工作抽查机制以及建立质量问题全面举一反三机制等对策和建议。
关键词: 归零、分级管理、最佳实践
引言
航空武器装备特有的多品种、技术含量高、涉及专业领域广、组成和结构复杂、配套关系复杂、技术难度大、风险因素多、质量要求高、研制周期短等特点,决定了产品质量问题的复杂性和多样性。在质量监督过程中如果不能具体问题具体分析,而是生搬硬套有关条条框框,可能会严重影响航空装备研制,不能适应新时期武器装备跨越式发展的需要。如何严格按照GJB 5711-2006《装备质量问题处理通用要求》快速有效地开展质量问题的归零工作,以确保航空武器装备不带风险使用,是需要航空人不断实践总结、深入探讨的重要课题。
装备质量问题是指装备质量特性未满足要求而产生或潜在产生的影响或可能造成一定损失的事件。质量问题发生后,需要从技术、管理上分析问题产生的原因、机理,并采取预防或纠正措施,以避免问题重复发生,即质量问题的归零。其具体内容体现在“双五条”标准中,包括质量问题技术归零的五条标准和管理归零的五条标准。质量问题“双归零”孕育于航天领域质量形势严峻的20世纪90年代初期,诞生于航天事业发展陷入低谷的90年代中期,成长于航天事业走出困境并步入蓬勃发展轨道的90年代中后期。从技术归零到管理归零,质量问题“双归零”方法的提炼和形成,经过了一个自我吸收、自我发展、不断完善的过程。质量问题的归零过程,是实现质量管理从事后的问题管理转化为事前的预防管理的过程。质量问题“双归零”管理方法,对产品本身是“救火”措施,对其他型号起“防火”作用。由于“双归零”的科学性、先进性和有效性,其已被广泛应用到多个技术领域,并已成为 GJB 5711-2006 《装备质量问题处理通用要求》的重要指导原则。
关于“双归零”的演变过程,最初来源于美军标的FRACAS系统,传统的FRACAS主要是针对个体事件采取的就事论事的狭义方法,而“双归零”则是以个体普及整体、以典型涉及全面的广义方法,能够很好地弥补质量管理体系缺漏项,对把质量问题由单纯的事后处理转变为事后与事前预防相结合的效果最为明显。“双归零”的方法是按照戴明、朱兰、克劳士比和费根堡姆共同的“质量改进”主题,遵循着戴明循环(PDCA),从出现的质量问题入手,通过技术上的分析、管理上的改进,达到系统预防的目的。而今,“双归零”在航空、电子、兵器等其他行业得到了广泛推广和应用。2011年“双归零标准”的基础上航天提出了“眼睛向内、系统抓总、层层落实、回归基础、提升能力”的“新五条”归零原则[1]。
1 当前航空武器装备质量归零工作存在问题
目前航空武器装备质量问题归零工作已经形成了比较系统、规范的组织、制度和方法体系。但近年来,随着型号研制任务的急剧增加,航空武器装备质量问题归零也面临着一些新的问题。
1.1问题收集不全,哪些问题需闭环/哪些问题需归零划分不清
航空产品全寿命周期问题应包括设计过程发生的问题、设计评审和复查中发现的问题、制造中发现的问题、试验中暴露的问题、试飞和靶试中发现的问题以及航空产品外场使用中发现的问题。问题往往收集不全,也未明确哪些问题需闭环,哪些问题需归零。
质量问题归零和质量问题闭环的本质是相同的,均为解决质量问题,有效实施质量改进的管理方法。本文理解闭环包含归零。归零是闭环的一部份,是闭环活动中一种具有航天/航空特色的特殊形式。闭环活动适用于所有质量问题,而归零活动的应用范围有限定。归零应比一般闭环活动更深刻,更规范。简而言之,归零是闭环的高级形式。闭环和归零的关系,如图1所示。
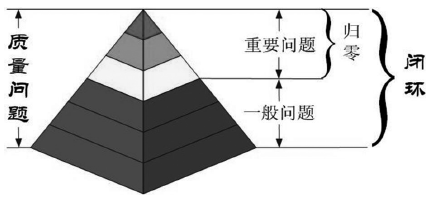
图1 闭环和归零的关系图
在实际科研生产过程中,质量问题繁杂且零散,出现一般质量问题的数量不在少数,大约占总数的60%。若一般质量问题也按照归零要求进行,有“杀鸡用宰牛刀”之嫌,效率不高,如“勘误性错误导致图文物不一致”的质量问题。质量问题处理尺寸过严,“归零”有被滥用和实施不畅的现象。反之过松,需归零的问题按一般流程处理或归零过程出现意识滑坡、职责权限不清、敷衍了事的情况,会导致问题剖析不到位和解决不彻底,隐患依然存在。
1.2 面对问题,眼睛向外导致问题原因定位不准确
基于国防科学技术和国防工业水平以及人类认识本身的局限性和渐进性,武器装备研制不可能一帆风顺,难免出现一些技术和质量问题。很多大型武器装备一经立项,就面临进度紧、任务重、困难多的研制形势。在这种情况下,无论是研制单位还是军方都不希望出现技术和质量问题,将一次成功作为追求目标。为确保试验成功,不出问题,试验通常都在非常理想的环境和条件下进行,很少在武器装备作战使用的边界环境和条件下开展试验,导致很多作战使用性能和战术技术指标得不到验证和考核,研制出来的武器装备不能满足实战需要。但在实际归零过程中,受时间、进度、归零成本等因素的影响,存在总体单位不愿承担责任的现象;同时,由于分系统、组件配套单位受承揽任务压力的影响及经济利益的驱动,存在敢怒不敢言、委曲求全、主动背黑锅等问题[3]。
1)回避总体问题,倾向于归结为分系统和组件问题。
一旦研制中出现技术和质量问题,研制总体单位容易出现难以正确地认识和对待这些问题,回避总体问题,倾向于归结为分系统和组件问题。Q/QJA10《航天产品质量问题归零实施要求》规定:“难以分清设计和生产责任时,由型号总指挥确定归零单位;难以分清分系统间责任时,由总设计师确定归零单位;难以分清组件间责任时,由系统技术负责人确定归零单位;难以分清总体和系统责任时,由总体单位归零;难以分清系统和组件责任时,由系统单位归零”[2]。
2)回避设计问题,倾向于归结为低层次的操作问题。
通过对近年来发生的工艺、操作等问题的分析发现,部分问题在归零时存在回避设计问题,倾向于归结为低层次的操作问题的现象[4]。其中,工艺问题中不乏设计不合理、设计生产性考虑不充分的问题,但却很少从设计角度进行改进;操作问题中,有近50%的问题是由于设计(含工艺设计)不当导致的误操作问题,设计可生产性差,操作人员在产品实现时难以操作、无法操作的问题较为突出,但这类问题在归零时一般都简单地归结为操作问题。
当然也存在着现实的客观情况。若定位为设计问题,纠正措施将为设计更改或修订管理制定。随后将开展办理更改单及制成品处理、落实产品设计更改等后续工作。按现行型号技术状态管理要求,若部队已装备,需逐级向上级单位专题汇报,并编制技术通报,增加大量的管理成本。反之定位为工艺问题,则上述工作均可免除。
3)回避单位自身问题,倾向于归结为外协外购单位问题。
近年来,外协外购的问题较为突出,所占比例一直在30%以上。对于外协外购的问题,一般由外协外购产品厂家进行归零,很少有任务委托单位自身开展归零工作的,总体单位因为分系统、组件产品质量而自身开展归零的更是寥寥无几,“眼睛向内查找自身问题”成了一句空话。
4)回避管理问题,倾向于归结为技术问题。
近年来,由于加大了对管理问题的整治处罚力度,并实施“零容忍”,个别单位在出现问题时,往往用技术归零代替管理归零,真正的管理归零活动很少。
即使定位为管理问题,纠正措施大部分的问题仍以技术上的改进和完善为主,在管理方面采取的改进措施针对性不强。但管理问题往往需考虑体制机制、各级责任、技术和管理流程优化、技术储备和条件保障等方面分析问题背后的深层次管理原因[5]。非某个人或某个部门之力就能解决,若主管所领导不予重视,许多管理问题很难从根上解决。反之定位为技术问题,则上述工作均可免除。
1.3 过于强调快速归零导致归零不彻底
为了适应型号高强度密级训练任务的需要,有些单位在归零工作进展缓慢时,为满足进度需要,甚至存在淡化问题或是伪归零现象,这些情况都会严重影响装备研制质量,给装备埋下重大隐患。
1.4举一反三不全面
举一反三不全面有主观和客观原因:
1)主观上不想开展举一反三工作。随着型号研制任务的不断增加,产品一旦出现质量问题, 特别是组件及以下级产品出现质量问题,如全面开展举一反三工作任务将十分繁重。目前,除元器件批次问题快速响应、涉及部队外场型号举一反三等强制要求外,大部分的举一反三工作都是型号系统自发组织的。但全面开展举一反三工作,会占用型号系统大量的时间和精力,致使个别型号或组件单位主观上不想开展全面举一反三工作,存在侥幸心理。
2)跨型号、跨单位举一反三工作难以开展。受技术秘密、任务竞争等因素的影响,跨型号、跨单位的质量问题举一反三工作一直难以开展。开展举一反三工作,必须明确问题的定位、故障机理和问题产生的原因,这些都是分系统、组件级单位,甚至是总体单位不愿意公开的核心技术秘密。但没有这些信息,跨型号、跨单位举一反三工作就是一句空话。
2 加强航空武器装备质量问题归零工作的几点建议
航空武器装备发生质量问题后,在技术上、管理上进行彻底的“双归零”,是保证航空事业持续健康发展的重要手段。面对新的形势和新的问题,必须要从顶层着手进行策划,创新工作机制,用科学的方法来指导新时期的归零工作,确保归零工作的有效性。
2.1营造良好的质量文化氛围
1)营造人人暴露质量问题的导向。
质量数据是开展举一反三工作的基础,只有质量数据全面且真实,才能保证后续工作顺利开展。结合本单位质量信息录入已实现全面信息化的基础上,允许各部门每个人均可在设计、生产、交付及排故的任何阶段发现质量问题均录入质量故障信息系统。质量文化建设中落实相关处罚及奖励政策,对于试飞、调试时发现问题不报者时需进行警告;对于信息录入全面完整且主动发现问题者需给予奖励,纳入质量诚信管理。
2)营造质量问题彻底归零的导向。
对于由于过分强调快速归零而导致的归零不彻底、质量问题重复发生的,要加大处罚的力度,给责任单位、责任人予以处罚;经过验证,确实实现了彻底归零的问题,要予以奖励,与人员考核及升职绩效打分挂钩。
2.2建立质量问题分级处理制度
表1 质量问题的分级处理表
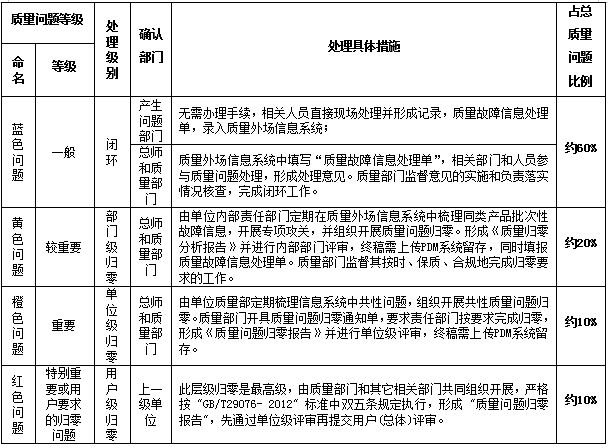
结合本单位工作实际,依托质量外场信息系统故障源,制定了问题分级处理管理制度,本文简要的提出质量问题分级处理和具体实施措施,详细内容如表1所示。
通过质量问题分级处理制度的实施,质量部门主管无需组织大量技术归零会的流程性工作。质量部门主管工作重心由原先参与其中,转变为开展产品质量趋势分析和监督过程符合性检查。
质量部门可建立了质量问题归零工作抽查机制,成立质量问题归零工作监督检查机构,定期按比例对近期完成归零的问题进行抽查,重点审查其归零的正确性、纠正及整改措施落实情况,以及举一反三情况。对于发现的明显归零不彻底、归零不正确的问题,要追究责任单位和评审专家的责任。同时纳入质量诚信管理档案。该做法可推广至集团公司和各级主机部门。
为了强化质量问题管理原因分析,避免管理归零措施庸俗化,质量部门需建立典型问题管理原因分析机制。对于重大质量问题、典型的管理问题,以点带面,全面查找质量管理体系中存在的薄弱环节,建立能力提升专项课题,制定有效的整改措施和实施计划,全面提升质量管理水平。
2.3建立最佳归零实践库,逐步迭代更新各类产品FMECA报告
对于技术归零工作,应在建立各级各类产品故障模式库的基础上,建立针对不同产品、不同故障模式的技术归零报告模板,整理技术归零最佳实践,供后续归零工作参考。已归零的问题,需定期开展迭代更新产品的FMECA,为后续产品故障分析提供数据支持。
对于管理归零工作,要紧紧抓住“过程清楚”这一基本原则,只要把问题产生过程切切实实地描述清楚了,明确到具体流程、岗位、人员及文件和要求,管理归零工作就容易入手了[5];同时,要对质量问题的管理原因进行准确分类,可以考虑从质量管理体系的角度出发,将质量问题的管理原因分为策划、职责落实、能力与意识、制度和流程、组织协调、监视和测量、技术储备与发展、保障条件建设、持续改进机制9个方面,并强制要求责任单位务必从上述9个方面全面开展管理原因分析工作,并制定针对性的改进措施。
2.4 建立质量问题全面举一反三机制
为了避免质量问题的重复发生,全面、科学的举一反三工作至关重要。为了确保万无一失,当前的举一反三工作,往往是过分强调了全面性,而忽略了科学性。“一人得病,大家吃药”,但“药”吃得太多、吃的人范围太广,对本“没有病”的人也带来了不利影响。因此,要做好全面的举一反三工作,同时科学合理地设定举一反三的范围。
1)举一反三的信息源要全面。要利用信息化系统如本单位使用的质量外场故障信息系统,全面收集型号研制过程中发生的质量问题信息。同时,要打破跨研究院/所、跨型号质量问题信息传递不畅的问题,在符合保密要求的情况下,允许跨单位、跨型号的信息查询与浏览,特别是要放开质量问题归零报告的查询浏览权限。
2)举一反三的范围要科学。目前的举一反三工作,集团公司、研究院/所基本没有统一的安排,全靠型号和各单位的自觉,其效果有限。对于集团公司、研究院/所,应建立全面举一反三的工作机制,委托专家,定期对所有的质量问题进行梳理,明确需要开展举一反三工作的问题清单, 以及举一反三的范围,并以通知、通报等形式,下发各有关单位开展举一反三工作。除了技术归零要开展举一反三工作外,建议对于典型的共性管理问题,也应全面开展举一反三工作。
本单位做法为质量部门定期梳理共性问题。在总师例会中确认拟开展举一反三的问题条目。由质量部门牵头组织,由各型号主任设计师商型号总师确认范围,部门质量员追踪落实情况并汇总上报质量部们。质量部门将监督结果定期在调度会上向所领导汇报。
2.5 建立质量问题归零的组织与评判准则
目前质量问题归零工作仅依据GJB 5711-2006 《装备质量问题处理通用要求》还远远满足不了实际工作需求。各单位需根据实际情况制定质量问题归零的组织与评判准则。明确各项工作开展时各部门的职责划分;明确走正式归零程序的问题范围;明确各类不同级别问题闭环结束形式及证据;明确技术归零转入管理归零的入口准则;明确管理归零报告要求单位行政正职签署;明确将管理归零的程序、案例作为各级领导质量培训的内容;明确型号阶段节点上需对前期归零工作进行监督检查等。该准则制定和落实保证了归零工作执行质量。
3 结 束 语
装备质量问题归零实施要求已使用十多年,经实践验证成功、有效,为彻底消除质量隐患、解决质量问题和避免问题的重复发生提供了一套比较系统和科学的程序、方法。
但在实际型号科研生产过程中,实际存在归零使用随意和使用不畅的现象,此现象人为地破坏了“归零”的严肃性和权威性,同时不利于在其它军工产品领域推广。对质量问题的处理,尺度过严或过松,均不能达到理想的效果。只有做到恰到好处“量刑适用”,才能更好更高效地达到期望效果。本文提出了营造良好的质量文化氛围、建立问题分级管理、建立归零最佳实践、建立典型问题管理原因分析机制、建立质量问题归零工作抽查机制以及建立质量问题全面举一反三机制等方法,还有不足之处,尚需在长时间实践中检验、验证和不断完善。
参考文献:
[1] 张陶, 刘志卿. 航天质量问题归零管理的历史追溯和发展[J]. 质量与可靠性, 2013 (3) :24-26.
[2] 中国航天科技集团公司科技质量部 航天产品质量问题归零实施要求: Q/QJA 10 [S]. 北京:中国航天科技集团公司, 2002: 2-3.
[3] 孙涛, 过康瑛. 浅析质量问题技术归零工作的有效性 [J]. 航天工业管理, 2013 (8): 8-10.
[4] 曹克勇, 张英志. 对型号产品质量问题管理归零工作的认识 [J]. 航天工业管理, 2014 (10):10-12.
[5] 樊灵芳. 贯彻质量问题归零两个五条标准的认识与体会 [J]. 质量与可靠性, 2000 (3): 13-14.